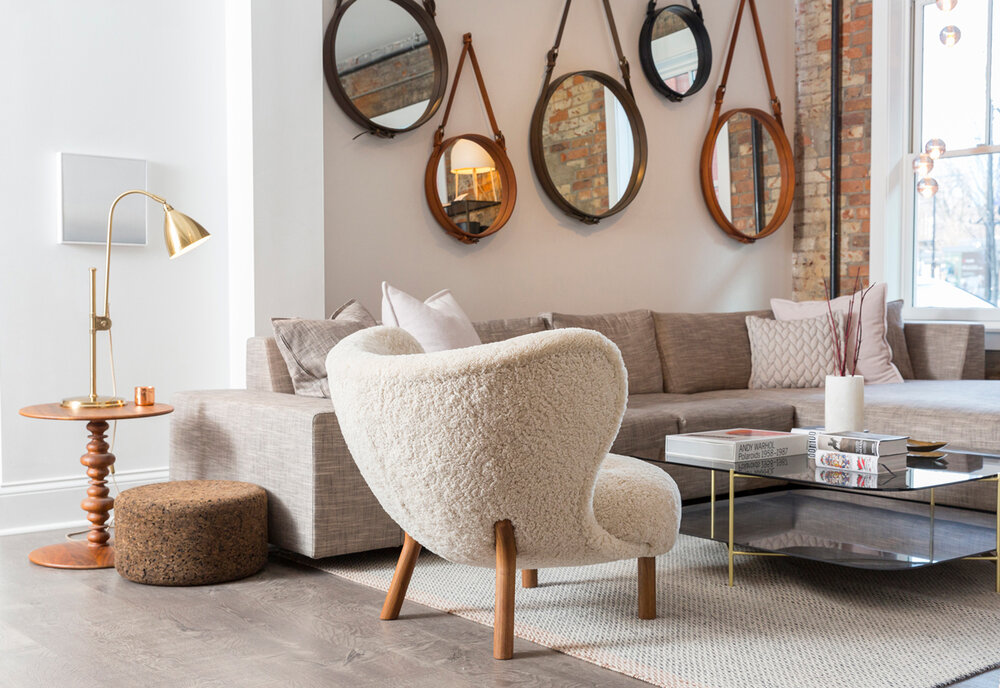
Izdelava tlaka in ometa
Pri gradnji hiše se z uporabo tlaka ali ometa obvezno srečamo vsaj nekajkrat. Čeprav se nam zdi, da o tem nam ni potrebno kaj dosti vedeti, hitro nastopi težava z izbiro ustreznega materiala in načina izvedbe.
Medtem, ko smo pri gradnji ali adaptaciji stanovanjske hiše pozorni na celo vrsto detajlov, pa marsikdaj pozabimo sicer na prvi pogled samoumevna gradbena posega kot sta izdelava tlaka in ometa. Zaradi tega prihaja pri njihovi izvedbi marsikdaj do nemalo težav in zapletov, ki lahko pustijo na bodočem domu tudi trajne posledice.
Izdelava notranjega tlaka
Ker se med betonsko podlago in tlakom vgradi izolacijo, se doseže precej boljšo toplotno in zvočno izolacijo prostorov. Poleg tega betonski tlak izenači različne višine tal v prostorih. Odvisno od posameznih prostorov je namreč običajno nekaj centimetrska razlika med zgornjo višino grobe betonske podlage in bodočo končno višino talne obloge. Ta razlika je odvisna od bodoče uporabe debeline talne obloge. Seveda pa si želimo, da bi bila končna višina tal v vseh prostorih enaka, saj bi se s tem izognili nepotrebnih prestopanj in spotikanj ob talno podlago pri prehodu prostorov. Vgrajeni tlak ta problem če že ne odpravi, vsaj omili. Izraz notranji tlak je poznan tudi pod imenom estrih. Beseda estrih izvira iz nemškega jezika, kar pomeni zadnjo roko pri zaglajevanju površine tlaka. S sedanjo tehnologijo in uporabo različnih materialov proizvajalci ponujajo že veliko število različnih vrst estrihov, ki se razlikujejo tako po materialu kot izvedbi. Glede na debelino estriha in uporabo veziva je poznan cementni estrih, samorazlivni estrih na osnovi kalcijevega sulfata (anhidritni estrihi) in izravnalna masa oziroma polimerni cementni nanos. Pri stanovanjskih objektih se daleč največ vgrajuje cementni estrih. Na cementni tlak je običajno položena zaključna talna obloga. V kleti, garaži ali delavnici pa je lahko tudi kot končna talna površina. Cementen estrih je sicer vodoraven sloj drobnozrnatega betona. Ta je v osnovi pripravljen v kombinaciji cementa, vode in peska. Izbira peska je precej pomembna za kakovosten estrih. Praviloma se uporablja naravno sejani pesek granulacije do 4 mm. V primeru uporabe nečiste in mlete separacije peska, je uporaba cementa za polovico manjša kot je po predpisanih normativih, kar seveda ni pravilno. Za kakovosten estrih je treba nujno uporabiti ponovno separacijo peska in približno 45 do 50 kg cementa na en mešalec. Ne tako daleč nazaj so se za armiranje cementnega tlaka uporabljale kovinske armaturne mreže. Njihova montaža je bila zamudna. Poleg tega je bilo potrebno paziti, da se mreže niso na nobenem mestu dotikale tal. Danes se za armiranje estriha poleg armaturne mreže uporabljajo sodobnejši materiali. To je jeklena mikroarmatura ali polipropilenska mikroarmatura. Ta se vmeša v betonsko zmes že med samim postopkom priprave betona, tako da se delci (vlakna) enakomerno porazdelijo po celotnem volumnu betonu. Z njihovo uporabo postane povezava betona trodimenzionalna in se zaradi tega zmanjša možnost razpok in lomov. Pravilen potek in dosledno upoštevanje vseh predhodnih del pred končno položitvijo tlaka je zelo pomembno pri postopku vgradnje cementnega estriha. Pred njegovo izdelavo je potrebno vgraditi vse vratne in okenske okvirje, vse vrste inštalacij in tudi izdelati omete. Ravno tako morajo biti opravljena vsa pleskarska dela, razen zaključne faze. Betonska plošča mora biti v celotni debelini ustrezno suha in brez umazanije. Če je na betonski plošči vgrajen inštalacijski razvod, mora ta biti pritrjen na betonsko podlago in zalit z izravnalnim slojem, ki sega do vrha razvoda po celotni površini prostora. Najprej na grobo betonsko podlago položimo izolacijski material. To je lahko stiropor, kateri je dober toplotni izolator, ali izolacija iz kamene volne, ki je boljša za zvočno izolacijo. Vsekakor bo ustrezna izbira izolacije vplivala na porabo ogrevalnega vira. Ena od možnosti za polaganje izolacije med inštalacijske cevi, ki so na betonski plošči je stiroestrih. Lahko se položi tudi en sloj izolacije med cevi, drugi pa v nasprotno smer kot drugi sloj. Sam estrih se imenuje tudi plavajoči pod. To pa zato, ker se nikjer ne dotika stene in se s tem onemogoči prenos zvoka v zgornjo ali spodnjo etažo. To se doseže s položitvijo dilatacijskega stiropornega traku debeline 1 cm po spodnjih robovih sten. Pomembno je, da se povsod prepreči kakršenkoli dotik estriha s steno, kar bi povzročilo prenos zvoka. Ob tem se upošteva tudi dodaten prostor za njegovo raztezanje. Čez izolacijo prevlečemo PE folijo, ki prepreči navlaženje izolacije z vlago iz estriha. Na takšno pripravljeno površino se vlije armirani estrih. Debelina položenega estriha za stanovanjske prostore je ne glede na vrsto izolacije od 5 do 6 cm. To velja samo v primeru, če je estrih izdelan iz naravne separacije peska 0 do 4 mm in 45 do 50 kg cementa na en mešalec peska. Tako kot omet se tudi estrih lahko vgradi ročno ali strojno. Že več kot desetletje se tlake še v večji večini kot omete izdeluje strojno. Ti so tako glede kakovosti, natančnosti, časa izdelave in tudi cene izvedbe ugodnejši od ročne vgradnje. Danes se praktično že skoraj vsi graditelji stanovanjskih hiš odločajo za izvedbo strojnih tlakov. Strojni estrih se izvede s posebnim strojem, ki hkrati zmeša material in s pomočjo vgrajene črpalke transportira beton po posebnih ceveh do želenega prostora. Ker ima črpalka večjo moč, se beton lahko transportira tudi v višja nadstropja, kar je bilo pri ročni izvedbi precej naporno. Sveže vgrajen estrih je potrebno zaščititi pred prepihom, zmrzaljo in soncem, saj se mora posušiti povsem naravno in neprisiljeno. Le v tem primeru bo pravilno pripravljen za polaganje parketa, keramike ali kamna. Cementni estrih se suši do 60 dni, oziroma za vsak centimeter estriha od 10 do 15 dni. V primeru, da bo na estrihu položen parket ali laminat se mora estrih ob normalnih pogojih sušiti od 45 do 60 dni. 20 do 30 dni pa bo dovolj časa za sušenje estriha, če bo na njem keramična obloga. Za marsikoga, ki hoče pohiteti z vselitvijo v nove prostore, je to odločno predolgo, zato se je na trgu pojavila nova vrsta estriha, takoimenovani hitrovezeči estrih. Ta je izdelan z uporabo posebnih kemičnih veziv (hitrovezeči cement), s pomočjo katerega se tlak dovolj osuši že v 10-tih ali manj dneh. Je pa takšen estrih precej dražji kot klasični.
Epoksidni tlaki
Na trgu je v ponudbi velika izbira visoko odpornih tlakov. Med njih se uvrščajo industrijski tlaki s kvarc posipom, anhidritni estrihi, različni epoksidni tlaki, ipd. Ob takšni izbiri je potrebno upoštevati, da za boljšo kakovostjo tlaka stoji tudi višja cena. Takšni estrihi so namenjeni najbolj obremenjenim površinam kot so v industrijskih objektih, delavnicah ali na javnih površinah. Vse bolj pogosti pa so tudi v stanovanjskih hišah, kjer so večje obremenitve tal, kot so garaže, kleti, hodniki, kuhinje in kopalnice. Poleg visoke odpornosti na obremenitve mora zaključni tlak na obremenjeni omogočati še preprosto vzdrževanje. Če je ta končna talna obloga, mora izpolnjevati tudi dekorativno vlogo. Epoksidni tlak izpolnjuje vse te zahteve. V primerjavi s klasičnim tlakom ta (predvsem premaz) ponuja neomejene možnosti izbire barvnih odtenkov. Poleg tega se lahko v epoksidni sloj vgrajuje različne barvne ali svetleče lističe, ki podajo končni površini tlaka njegov edinstven in za njega značilen videz. Izbira se lahko še različno strukturo zaključnega sloja, ki je lahko gladka ali hrapava. Sijaj zaključne površine pa je zopet lahko s steklastim videzom visokega sijaja ali mat brez sijaja. Pri vgradnji epoksidnega tlaka je precej pomembna dobra priprava podlage. V večini primerov mora biti podlaga predhodno brezprašno peskana, brušena ali rezkana. Običajno je to betonska podlaga, lahko pa je tudi keramična, kamnita ali kovinska površina. Odvisno od debeline nanosa je poznanih več vrst epoksidnih tlakov. To je lahko impregnacija, zaščitni premaz, samorazlivni tlak, tlak maltnega tipa in epoksidni estrih. V stanovanjskih prostorih je uporaben predvsem zaščitni premaz, manj pa impregnacija in samorazlivni tlak. Epoksidni premaz je sestavljen iz epoksidne smole, trdilca in polnil. Poleg tega vsebuje še vrsto dodatkov kot so pospeševalci in zavlačevalci vezanja, dodatki za doseganje primerne razlivnosti, viskoznosti, itd. Takšen premaz izboljša mehansko odpornost betonske površine, poveča kemijsko odpornost, predvsem pa je dekorativno lepega videza in brezprašen. Poleg uporabe za hidroizolacijo se v namen talnega premaza lahko uporabi tudi tako imenovano polyureo. Ta lahko nadomešča tako epoksidne in poliuretanske samolive, kot tudi premaze (poliaspartska poliurea). Največja prednost takšnega premaza je v zelo dobrih fizikalnih lastnostih kot je visoka natezna trdnost, visoka elastičnost in tudi kemijska odpornost. Tako se lahko polyureo nanese tudi preko razpok in dilatacij. Z razliko od poliuretanov, predvsem pa od epoksidov, ta ne vsebuje polnil (čisti polimer). Ravno tako ne vsebuje topil. Njena značilnost je v izredno hitri polimerizaciji. Po nanosu je pohodna v 15-tih sekundah. S tem omogoča zelo hitro izvedbo del in predajo objekta v nadaljnjo uporabo. To velja zlasti v primeru, če se za zaključne premaze uporabi še poliaspartske premaze (prav tako izredno hitro sušenje). Na trgu lahko najdemo čisto polyureo, kot tudi hibridno polyureo. Slednja je cenejša, vendar ima nekoliko slabše lastnosti kot čista polyurea, vendar še vedno bistveno boljše lastnosti kot poliuretani in epoksidi. Polyurea je dvokomponentni material, ki se nanaša s posebno opremo. Črpalka segreje obe komponenti na 60 do 70°C in nato pod pritiskom obe komponenti ločeno potisne po ceveh do pištole za brizganje, kjer se obe komponenti v mešalni komori zmešata. Sama oprema omogoča prenos materiala po ceveh tudi do 120 metrov daleč. Epoksidna impregnacija je primerna za izboljšanje kakovosti betonske površine. V pore betonskih površin se penetrirajo čiste nizkoviskozne smole, kjer se strjujejo in s tem izboljšajo mehanske lastnosti površinske plasti. Na betonski površini s primerno kapilarno poroznostjo ali na tanki lasasti razpokani površini je najbolj učinkovita uporaba takšne impregnacije. Samorazlivni epoksidni tlak se uporablja zlasti v industrijskih objektih, kjer so tlaki mehansko in kemično precej bolj obremenjeni. Debelina takšnega tlaka je od 1,5 do 5 mm. Poleg pigmentov se za polnilo uporabljajo zlasti finozrnati kremenčevi peski in kalcijevi ali barijevi sulfati. Epoksidni tlak je primeren tudi za tlak v domači garaži, na parkirišču, v skladišču ali mehanični delavnici. Na takšnih površinah je vgrajen v debelini od 1,5 do 3 mm. Samorazlivni epoksi tlak z dodanimi barvnimi lističi v isti debelini je primeren za v prostor s srednje močno mehansko obremenitvijo in preplastitvijo betonskega tlaka. Zlasti od stopnje obremenitve, kateri bo tlak izpostavljen med uporabo je odvisna njegova ustrezna izbira. Ob tem se naj upošteva tako mehanske kot toplotne obremenitve. V smislu mehanske obremenitve so mišljene stopnja obtežbe epoksi tlaka, gostota prometa, obrus tlaka in udarci trdih predmetov. Ekstremne temperature, toplotni šoki in izmenično zamrzovanje ter odtaljevanje so dejavniki toplotnih obremenitev. Ob izbiri epoksi tlaka se naj upošteva tudi morebitni dvig kapilarne vlage v podlagi, agresivne kemijske reakcije z epoksi površino in njeno izpostavljenost UV žarkom. Seveda pa so dejavniki izbire tudi videz, barva in struktura epoksi tlaka, njegova nedrsnost ter enostavnost vzdrževanje in čiščenja. Različne vrste podlag in stopnje njihove dotrajanosti marsikdaj zahtevajo izbiro epoksidnega tlaka z različno kombinacijo materialov oziroma vrst smol in polnil. V primeru zapolnitve razpok v betonski podlagi ali zahtevi po visoki elastičnosti zaključnega tlaka je tako npr primerna uporaba kombinacije epoksi in poliuretanskih materialov. V zadnjem času se vse bolj namesto klasičnih epoksi smol z organskimi topili uporabljajo vodotopne epoksi smole, ki so ekološko precej bolj sprejemljive. Takšen epoksi material odlikuje njegova visoka paroprepustnost, dobre mehanske lastnosti in visoka kemična odpornost. Zaradi paroprepustnosti se njega lahko nanaša tudi na ne dovolj izsušeno betonsko površino ali na nehidroizolirano površino s kapilarnim dvigom vlage. V primeru novogradnje naj bo pred nanosom epoksidnega tlaka cementna podlaga dovolj suha. V kletnih ali pritličnih prostorih mora talna plošča imeti izvedeno kvalitetno hidroizolacijo. Ker je epoksidni tlak slabo paroprepusten, lahko sicer pride do odstopanja in luščenja tlaka. Ob uporabi epoksidnega tlaka pri adaptaciji stanovanjskih prostorov je potrebno biti pozoren predvsem na zadostno tlačno in površinsko natezno trdnost betonske podlage. Marsikdaj se zgodi, da v starejši stavbi slabo izveden betonski estrih ni primerna podlaga za nov epoksidni tlak. V tem primeru je potrebno predhodno utrditi podlago s penetriranjem niskoviskoznih smol ali z dodatno preplastitvijo visokopolimerizirane cementne malte.
Poliuretanska hidroizolacija
Balkon ali terasa sta neposredno izpostavljena različnih ekstremnim vremenskim. Če nista dovolj strokovno izdelana s pravilnimi uporabljenimi materiali, kaj hitro na izpostavljeni površini nastanejo razpoke, skoti katerega prične voda pronicati v beton in povzroči škodo. Trajna rešitev tega je le izvedba sistemske hidroizolacije, ki je dolgotrajno obstojna in odporna na vse vremenske vplive. V ta namen se priporoča uporabo poliuretanske hidroizolacijske mase. Ker je poliuretanski prekrivni sloj izdelan brezšivno, omogoča idealno zaščito pred pronicanjem vode oziroma vdoru vlage v konstrukcijski material. Poliuretanska masa je zelo elastična, ki s temperaturno spremembo ne izgubi svojih prvotnih mehanskih lastnosti. Svojo elastičnost tako ohrani od -40°C pa do +80°C. Na očiščeno podlago, ki je predhodno premazana s temeljnim premazom, se nanaša poliuretansko maso v tekočem stanju. Z nanosom prve plasti poliuretanske mase je potrebno z armaturno mrežico dodatno zaščititi vsa kritična mesta (stiki, dilatacije, sifoni, ipd). Zatem se nanese drugi sloj poliuretana. Poliuretanski premazi so v ponudbi z različnimi dodatnimi sestavinami. Posledično s tem so namenjeni za različne podlage. Za zunanjo dotrajano podlago iz keramičnih ploščic, teraca ali betona je npr. primeren barvni hidroizolacijski poliuretanski premaz, ki je pohoden. V namen dekoracije so lahko v njega dodani dekorativni lističi. Transparentni poliuretanski premaz je namenjen za zaščito slabo hidroizoliranega tlaka na balkonu ali terasi, kateri pa je dobro ohranjen oziroma še vedno dobro sprijet s podlago. Ravno tako se njega nanaša v dveh slojih. Opcija izbire je med svetlečim ali mat končnim slojem. Debelina nanešenega poliuretanskega premaza je od enega do dveh milimetrov. Premaz je odporen na UV žarke, z leti ne porumeni in ostane trajno elastičen.
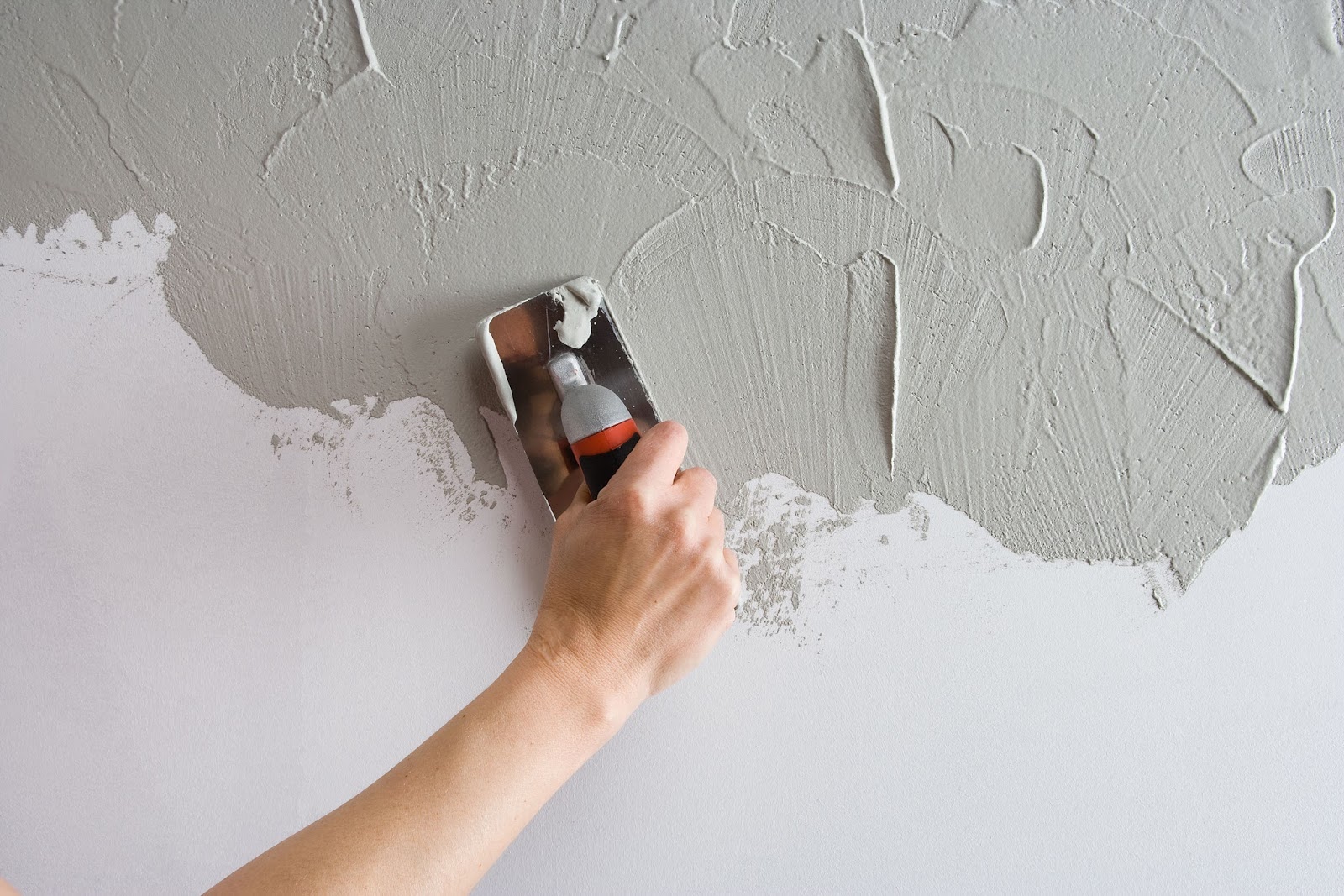
Notranji omet
Notranji omet na zidu ali stropu je preprosto obrazloženo neke vrste notranja obloga, ki ima predvsem dekorativno nalogo, saj zakrije gole zidake, betonsko ploščo in razvod inštalacije. Z njegovo izvedbo postanejo notranji prostori bistveno bolj atraktivni, zanimivi in pokaže se prva končna podoba bodočih bivalnih prostorov. Poleg estetskega videza, ometi opravijo tudi pomembno nalogo zaščite zidu. Tako kot ostali gradbeni posegi, so se tudi ometi skozi zgodovino spreminjali in izboljševali. V antičnem času so predvsem v južnih deželah uporabljali za omet malto iz gline. Že v stari Grčiji so za mineralno vezivo uporabili apno, s katerim so izdelovali zunanje omete odporne na vremenske vplive. Napredek pri ometih se je izboljšal že v rimskih časih, ko so pričeli uporabljati hidravlične materiale. Omet se je izboljševal vse do sredine prejšnjega stoletja, z iznajdbo Portlandskega cementa. Ta je v kratkem času postal hidravlično vezivo, s katerim se je pričel izreden razvoj raznih gradbenih materialov z visoko odpornostjo in obstojnostjo. Današnji sodoben omet mora vsebovati pravo mero hidravličnega veziva. To je lahko cement, apno ali mavec. Ravno po teh vezivih se ometi med seboj razlikujejo. Glede na uporabo veziva so ometi razdeljeni na štiri glavne skupine. Prva skupina so apneni ometi, izdelani iz gašenega apna. Apno je gašeno takrat, ko je ta odležal v apneni jami vsaj šest tednov. Odvisno od namena uporabe se razmerje peska in apna, ter velikosti zrn peska različno določa. Razmerje 1:2 do 1:3 je običajno pravilno za mešanico apna in peska pri notranjem ometu. V sedanjem času je bolj uporaben za vezivo izdelave ometa hidravlično apno. Ta je namreč za uporabo precej bolj praktičen, saj je tovarniško že pripravljen v vrečah in se ga na ta način lahko uporablja praktično kjerkoli in kadarkoli. Vsi apneni ometi imajo odliko, da so dobro prepustni in imajo sposobnost vpijanja vlage, ter tako delujejo kot nekakšni regulatorji vlage v notranjih prostorih. Naslednja vrsta so mavčni ometi. Ti so poleg gline najstarejše poznano maltno vezivo. Mavec je rudnina, ki jo pogosto najdemo v naravi na področjih, kjer so v preteklosti izginila morja. Medtem, ko lahko apnene omete uporabljamo tako na notranjih, kot zunanjih površinah, pa mavčne omete lahko samo v notranjih prostorih, ki so dovolj suhi. Pri uporabi mavčnega ometa je potrebno paziti, da se izdelano maso porabi že v nekaj minutah, saj se mavec kot vezivo zelo hitro strdi. Pomembna odlika tega ometa je, da se ne krči. Tretja skupina so cementni ometi. Ker so ti močno odporni proti vlagi in mehanskim poškodbam, so uporabni za veliko vrst različnih površin. Sam cement je sicer hidravlično vezivo, ki se ga izdela z mletjem žganega portlandskega klinkerja in mavca ter raznih dodatkov. Cementni omet se izdela v različnem razmerju uporabljenih materialov. Od 1:1 do 1:5, odvisno od tega ali je ta klasičen ali nepropusten omet. Ob tem je potrebno omeniti, da cementni omet na opečnati podlagi zelo rad razpoka, saj ima bistveno drugačno razteznostno lastnost kot opečnati zidaki. Zaradi tega se takšen omet uporablja predvsem na zidnih in stropnih površinah s pogostim močenjem, kjer je potrebno zadostiti višjim zahtevam po trdnosti, odpornosti na vlago in na zmrzal ter dobremu tesnjenju. Možna je uporaba tudi kombinacije omenjenih ometov. Izdela se lahko apneno mavčni ali apneno cementni omet. Predvsem slednji se na zidovih stanovanj med vsemi ometi največ uporablja. Razlog tega je v tem, da takšen omet združuje odlične lastnosti cementa, z visoko trdnostjo in dolgotrajno obstojnostjo, ter zmes apna, ki bistveno pripomore k lažji izvedbi. Torej kombinacija ometov zadržuje vse pozitivne lastnosti dveh različnih veziv. Najmlajša vrsta ometov so tako imenovani suhi ometi. Ti so zaradi svoje praktične uporabe postali v kratkem času precej popularni. Suhi ometi so kot končni izdelki izdelani že v tovarni. Pakirani so v vrečah po 50 kilogramov. Za pripravo se takšnim ometom doda le še vodo. Suhi omet se lahko nanaša le na predhodno podlago iz apneno cementnega ometa. Sam način izvedbe ometa je v zadnjih desetletjih zelo napredoval. Še do nedavnega se je uporabljal izključno klasičen ročni način nanašanja ometa z zidarsko žlico in gladilko. Ta se več desetletij in celo stoletja praktično ni spremenil. Z uporabo strojnih naprav pa se je marsikaj spremenilo tudi pri tem gradbeniškem postopku. Nekdaj so se tako imenovani strojni ometi uporabljali le v večjih industrijskih in blokovskih zgradbah, medtem ko si lastniki družinskih hiš tega niso mogli privoščiti, saj so bili takšni načini ometavanja površin bistveno dražji od delovne ure zidarja s klasično zidarsko žlico in gladilko. Že precej zadnjih let pa se je tovrstno razmerje močno spremenilo v prid strojnemu ometavanju. Zato se sedaj njega tudi graditelji hiš najbolj poslužujejo. Razlika med klasičnim in strojnim nanosom ometa je poleg neprimerno hitrejše izvedbe tudi v tem, da je omet z strojno izdelavo kakovostnejši. Vsa malta gre namreč skozi vibracijsko mrežo, kar pomeni, da je bolj »mastna« in s tem bolj kompaktna. S tem je omogočena možnost tudi debelejšega nanosa ometa. Kakovost ometa je odvisno poleg načina postopka in sestave veziva tudi od vrste in stanja podlage ter vremenskih razmer pri pripravi in izvedbi. Pomembno je, da v času nanosa ni prehladno, saj v mrazu sveža malta zmrzne in s tem izgubi moč vezanja. Tudi vročina ni primerna za izdelavo ometov. V vročem okolju lahko iz vlažnega ometa prehitro izhlapi voda, katera je sicer potrebna za vezanje materiala. S tem pride do razpok na ometu. Najboljše razmere za ometavanje zidnih in stropnih površin so v jesenskem in spomladanskem času. Vrsta in stanje podlage je za kakovosten omet tudi precej pomembno. Z nanašanjem ometa se lahko prične šele, ko se zidovi dovolj osušijo. Najprej je potrebno zidove očistiti prahu in izravnati izbokline od malte, ki nastanejo pri zidanju. Opečne zidove je predhodno potrebno navlažiti z vodo, saj bi lahko v nasprotnem primeru opeka potegnila iz maltnega ometa vlago, ki je potrebna za vezanje. V primeru, da so stene izpostavljene ponavljajočemu zamakanju, se naj uporabi neprepusten omet, sicer bo lahko podlaga vpijala vlago. Nastala zbrana voda pa pri nizkih temperaturah lahko zmrzne. Da ima omet sposobnost maksimalno dobrega oprijema na podlago, morata omet in podlaga imeti čim bolj enak razteznostni koeficient. Predvsem leseno ali kovinsko podlago je potrebno zaščititi z ustreznim premazom ali lepenko, da omet ne razpoka. Ometavati je možno tudi materiale za toplotno izolacijo ter gladke obložene plošče. Vendar ob posebni pripravi podlage in s posebnimi vezivi. Razlika med ročnim in strojnim postopkom nanosa ometa je tudi v številu nanosov. Ročno nanašanje poteka v treh nanosih. Cementni obrizg, grobi nanos in fini nanos. Pri strojni izdelavi se opravi samo enkraten nanos. Material se zmeša v posebnem stroju in se ga strojno preko cevi transportira neposredno na površino. Nanaša se ga v obliki vodoravnih črevastih nanosov, ki se jih razvleče po celi površini. Poleg bistveno hitrejše izvedbe je prednost strojne izvedbe še v boljši kakovosti ometa in čistejšem načinu izdelave. Pripravljeno mešanico za strojne omete pri nas izdeluje že kar nekaj proizvajalcev, ki nudijo tudi do 10 letno garancijo. Predvsem če gre za ometavanje večjih površin, je strojna izdelava ometov cenejši način v primerjavi z ročnim.
pripravil: M.A.